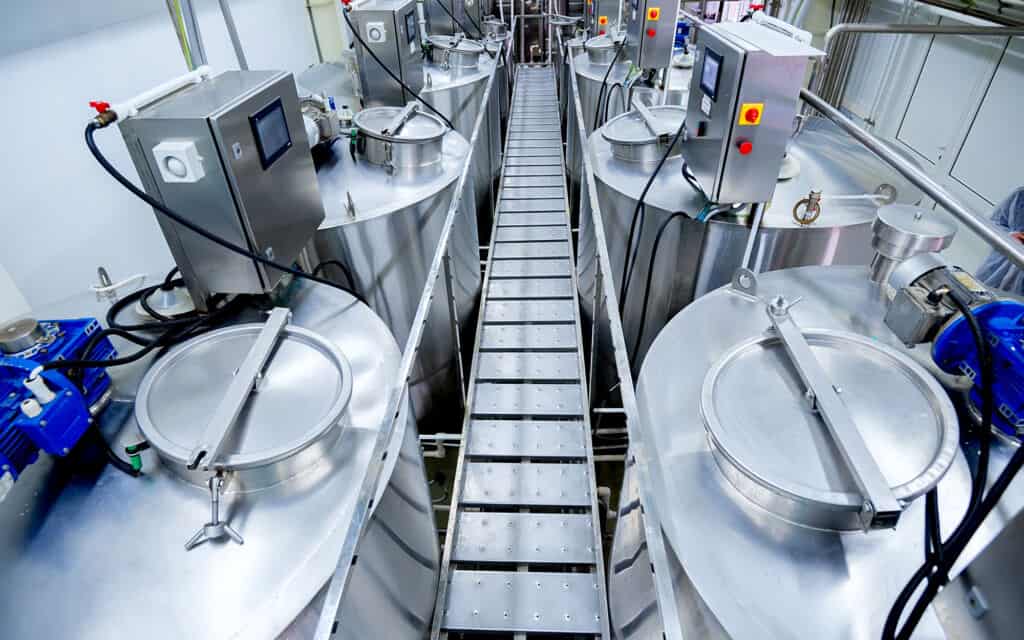
As the food and beverage industry continues to evolve, metal contamination has become an increasingly important safety issue. In order to prevent serious harm to consumers, it’s essential that food companies understand how to perform plant risk assessments that include identifying their foreign metal contamination risks.
Explaining Foreign Metal Contamination
Metal contamination can come from a variety of sources, including the environment, raw materials, ingredients from suppliers and processing equipment. The most common contaminants are fragments, including pieces or wear off metal machinery, wire mesh screen pieces, wear from rotary valves and conveying equipment, and metal fines. In some cases, even screws, nuts, and bolts, can find their way into the process!
Foreign Metal Contamination Guidelines
To reduce the risk of foreign metal contamination, both HACCP and FDA have a series of guidelines for food manufacturers. They advise regularly inspecting equipment and machinery for wear and tear, as well as using good manufacturing practices (GMPs) like appropriate safety equipment and protective clothing. Additionally, food manufacturers should ensure raw materials are checked for potential contaminants before they’re used in their production processes and that adequate protections are installed throughout the process to mitigate potential metal contamination risks.
How to Set Up an Efficient Foreign Metal Risk Assessment
To combat foreign metal contamination, an effective risk management program should include three essential parts:
- Prevention creates a hazard-free environment in your plant by implementing safety measures, such as providing employees with protective equipment and enforcing regular cleaning protocols.
- Detection focuses on finding any foreign objects in your product by using specialized equipment like metal detectors and food processing magnets.
- Investigation comes into play when a foreign object contamination incident occurs and the cause is determined to prevent its recurrence in the future.
Furthermore, one should examine the following steps in their supply and processing chains to perform a thorough plant risk assessment.
Suppliers
To evaluate how your suppliers prevent foreign metal contamination, start by considering the overall efficiency of their Hazard Analysis and Critical Control Point (HACCP) program. Next, identify if they have any specific steps in place to eliminate the risk of foreign objects, such as regular employee training and awareness programs. Suppliers should also be able to provide proof that third party validation reporting has been conducted at least annually by independent HACCP approved magnet validation specialists. If these types of programs exist, it’s important to assess their performance. Lastly, investigate the suppliers’ compliance history and look for any issues involving metal contamination and review their score rating (if available).
Receipt of Goods
Foreign objects can easily contaminate ingredients during the transportation process. To reduce contamination of your ingredients during transportation, check that the packaging, including seals and labels, is intact upon arrival. You should also make sure that your staff is properly trained in inspecting incoming goods. That way, they know what to look for in terms of contamination and how to properly handle goods if any problems arise. Documentation of magnet validity at final packaging should also be provided.
Processing and Packaging
To ensure your processing and packaging lines are as efficient as possible, consider installing camera inspection systems, metal detectors, X-ray scanners, color sorters, magnetic separators, and sieves to your production processes. Make sure to validate your systems and devices to guarantee their effectiveness and ensure they’re functioning properly at all times.
When it comes to food contamination in our supply chain, there’s more than meets the eye.
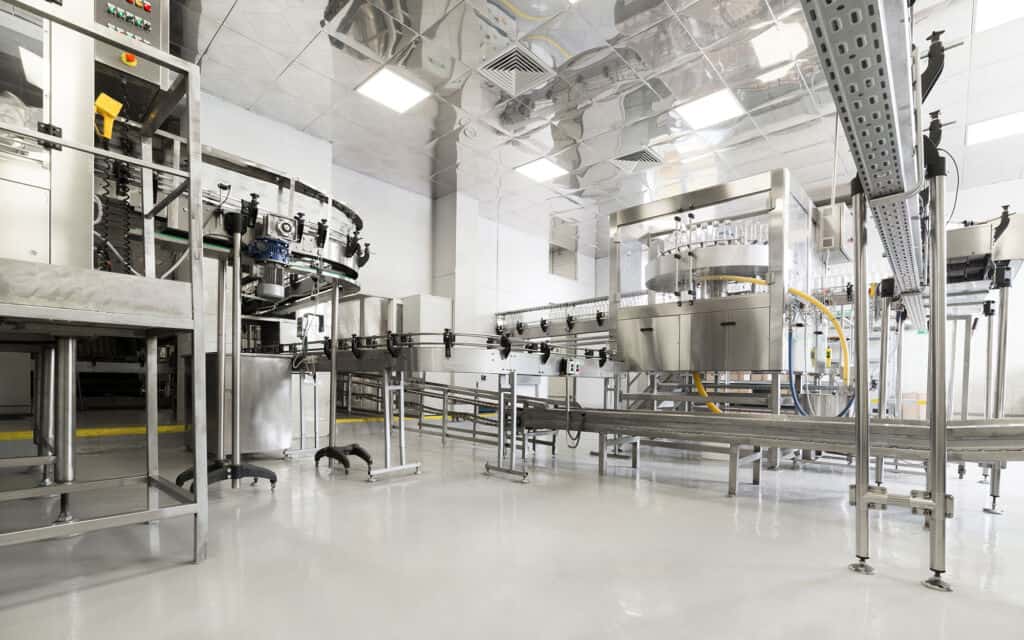
Using Metal Detection for Food Safety
Magnetic separators are used in several different stages of the food production process to remove contaminants from materials before processing and packing.
There are several types of magnetic separation equipment commonly used in the food processing industry:
Plate Magnets
Plate magnets are designed to detect and remove metal contaminants from products like grains, seed, and pet food. Capable of detecting even the smallest metal particles, plate magnets are effective at preventing contamination before the end of production and throughout the process, including protection of expensive machinery from damage and further metal contamination.
Drawer / Grate Magnets
Drawer or grate magnets are made up of a series of magnetic bars. As your product passes through, the magnetic bars collect and remove any ferrous metal contaminants present in the product. There are many grate magnet designs, such as the Mag-Ram® Self-Cleaning Separator or the Rapidclean® Drawer Magnet, suited to various product types, such as flour, grain, sugar, powdered ingredients and many more.
Rotary Magnets
Rotary magnets are an effective choice when it comes to handling dry, sticky, and difficult-to-flow products, such as dairy powders or sugar. These magnets are designed to create a powerful magnetic field that will help break up any clumps and prevent bridging.
Inline Magnets
Inline magnets come in a variety of designs that can be used for dry and wet applications, high-velocity product lines,pneumatic transfers, or liquid or slurry lines. Inline magnets are also suitable for pump lines, since they can help filter out any metal particles that could damage your system. Magnattack® has a variety of inline magnet designs, such as the Spherical Pneumatic Line Magnet, Powder Transfer Magnet, Emulsion & Slurry Magnetic Separator, and Pressure Pipeline Separator.
Key Takeaways
- To combat foreign metal contamination, an effective risk management program should include prevention, detection, and investigation.
- To perform a thorough plant risk assessment, consider your suppliers, monitoring your goods, processing and packaging lines.
- Magnetic separators are used in several different stages of the food production process to remove metal contaminants from materials.
Analyzing Your Processes With Plant Risk Assessments
At Magnattack®, our experienced technicians can come to your facility and work with your team to conduct a comprehensive plant risk assessment that involves studying a variety of critical factors, including:
- Process lines
- Ingredient entry and exit points
- Ingredients processed
- Historical foreign metal (FM) incidents
- Tonnage rates
- Effectiveness of existing magnets and metal detectors (if any)
- And more
Having a good magnet or metal detector in a poor location can be just as detrimental as having a poor one in a good location or not having one at all! If any existing magnets or metal detectors are ineffective or incorrectly installed, we can help you find the right solution to improve your foreign metal risk mitigation efforts. Contact us today to book an assessment with one of our experienced technicians.